| Double die flanging and automatic bottom and rings seamer
GENERAL CHARACTERISTICS
This transfer unit, sharing the base structure of a classic Klinghammer STAV175+S121, has been modified to improve almost every key point:
– The single inverter motor is replaced by two new brushless motors with encoding system in order to move star conveyors, dies and seaming head, reducing braking and starting times improving safety and productivity.
– Introduction of the new system KVSSS (Klinghammer Variable Speed Seaming System) this too operated by brushless motors, in order to tune and set the seaming cyles on bottoms and rings as desired.
– In combination with the new system a new double profiled seaming cam has been designed, guaranteeing a tight coupling at high speeds.
– Other brushless motors have been added with a crankshaft mechanism to operate the updated lid and bottom feeders.
– Automatic lubricating oil pump, for dieing and extraction mechanisms.
– New pneumatic system on all the extraction mechanisms, instead of using springs, it is possible to tune the strength of the cylinders as desired.
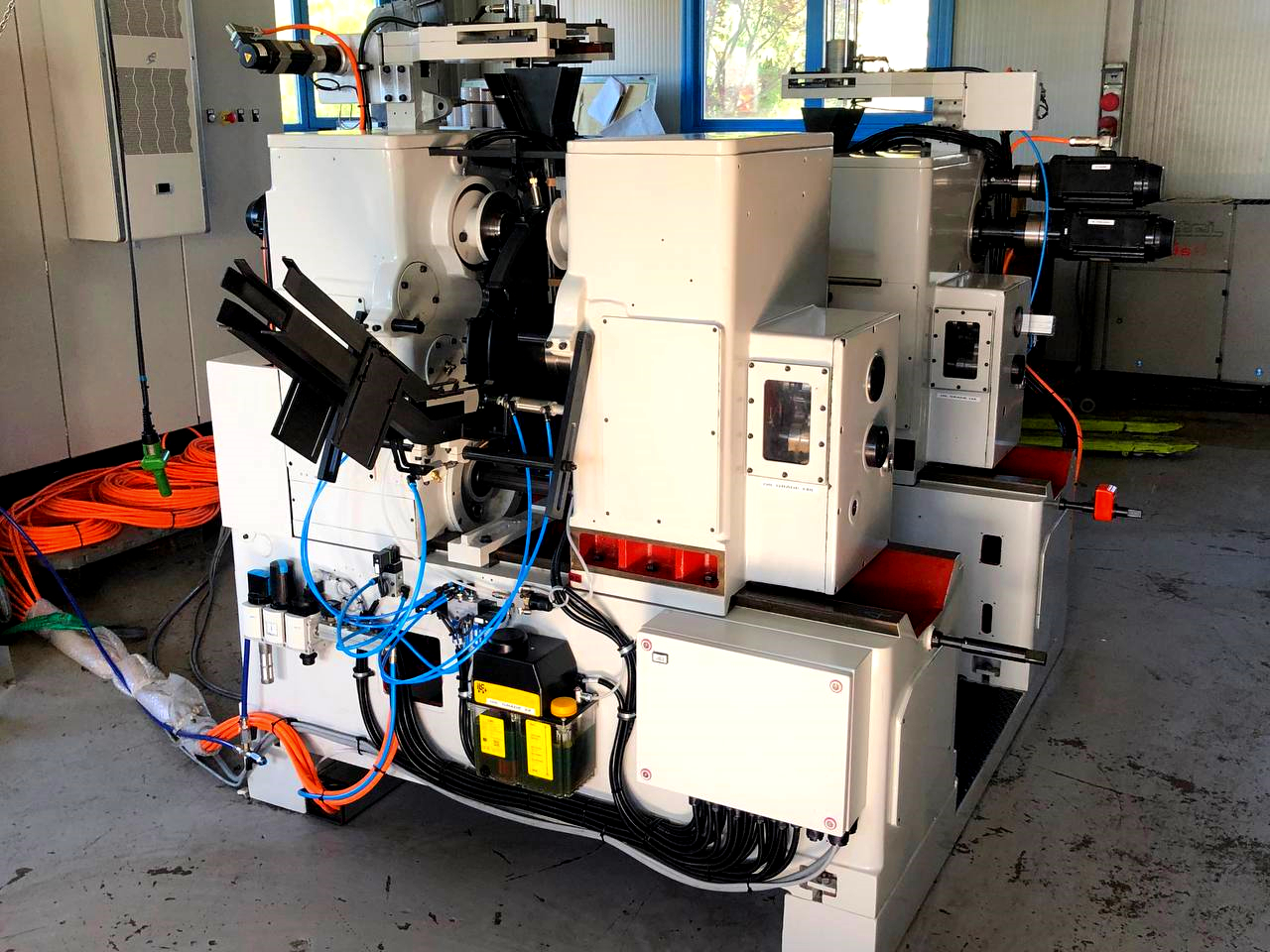
FUNCTIONING
The can bodies, placed in the inlet chute, pass to the star conveyors which transport them to the various stations. In the first, the flanging takes place at the ends simultaneously by means of two dies.
This system allows an exact calibration of the bodies, which is particularly recommended for the subsequent seaming of the bottoms and lids. At the seaming station the flanged bodies are transported by the star conveyors together with the bottoms mechanically fed by the blade picker. The seaming takes place when the can is stationary by means of a four-roller seaming head (two for the first and two for the second operation), which guarantees an absolutely safe closure. The seamed bottom cans are ejected by a special lever and cam on the integrated conveyor transport to lead them to the S121 module.
The movement of the cans and the feeding of the bottoms and rings are controlled by non-contact sensors, which control the stop of the machine in case of need. This occurs when there are no bodies, bottoms or when the conveying stars are subjected to excessive strain due to jamming (this also applies to the S121).
All the cams, the gears as well as the eight-position intermittent mechanism rotate in an oil bath. All fast-moving parts are mounted on ball bearings or needle roller bearings.
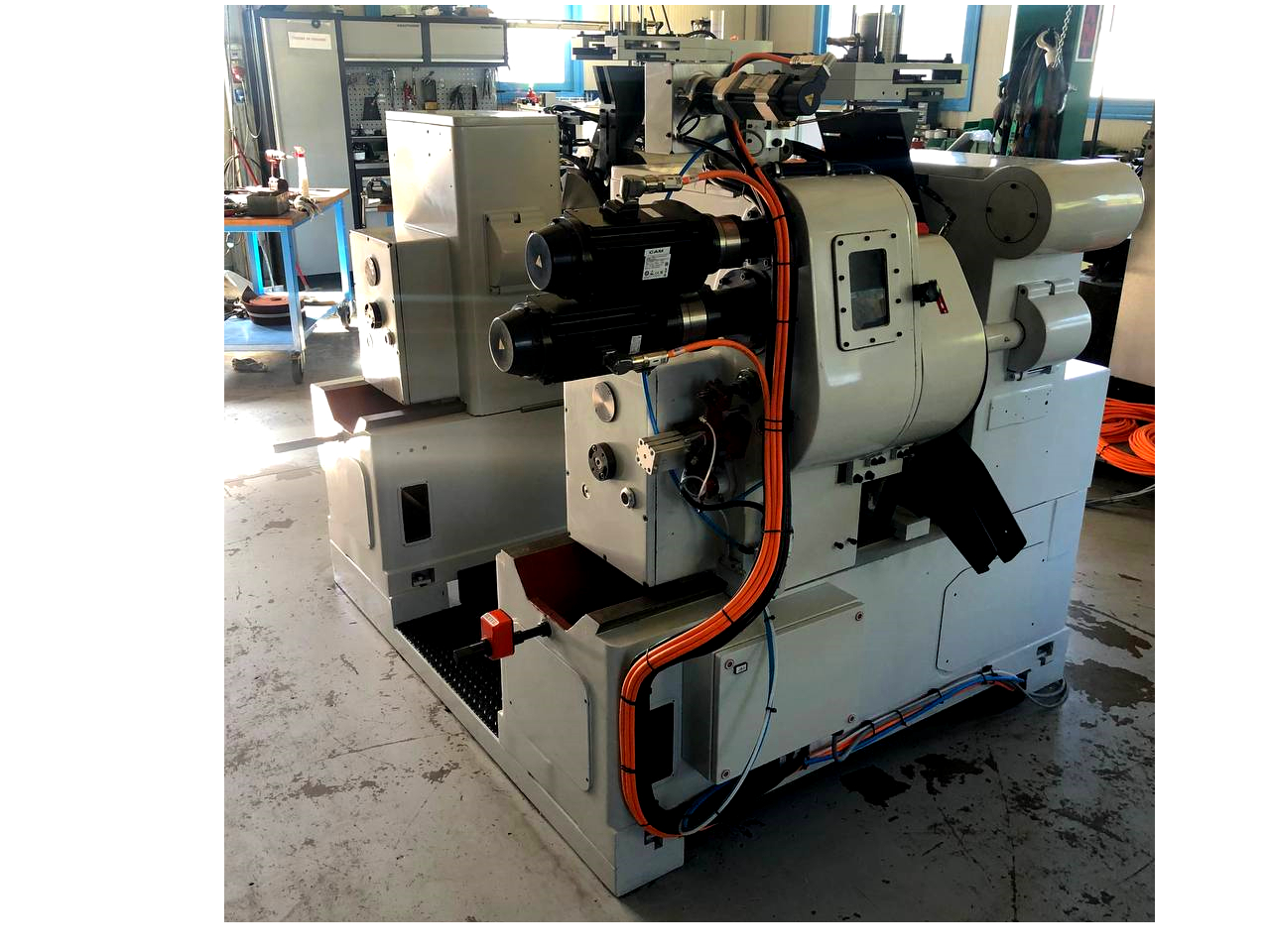
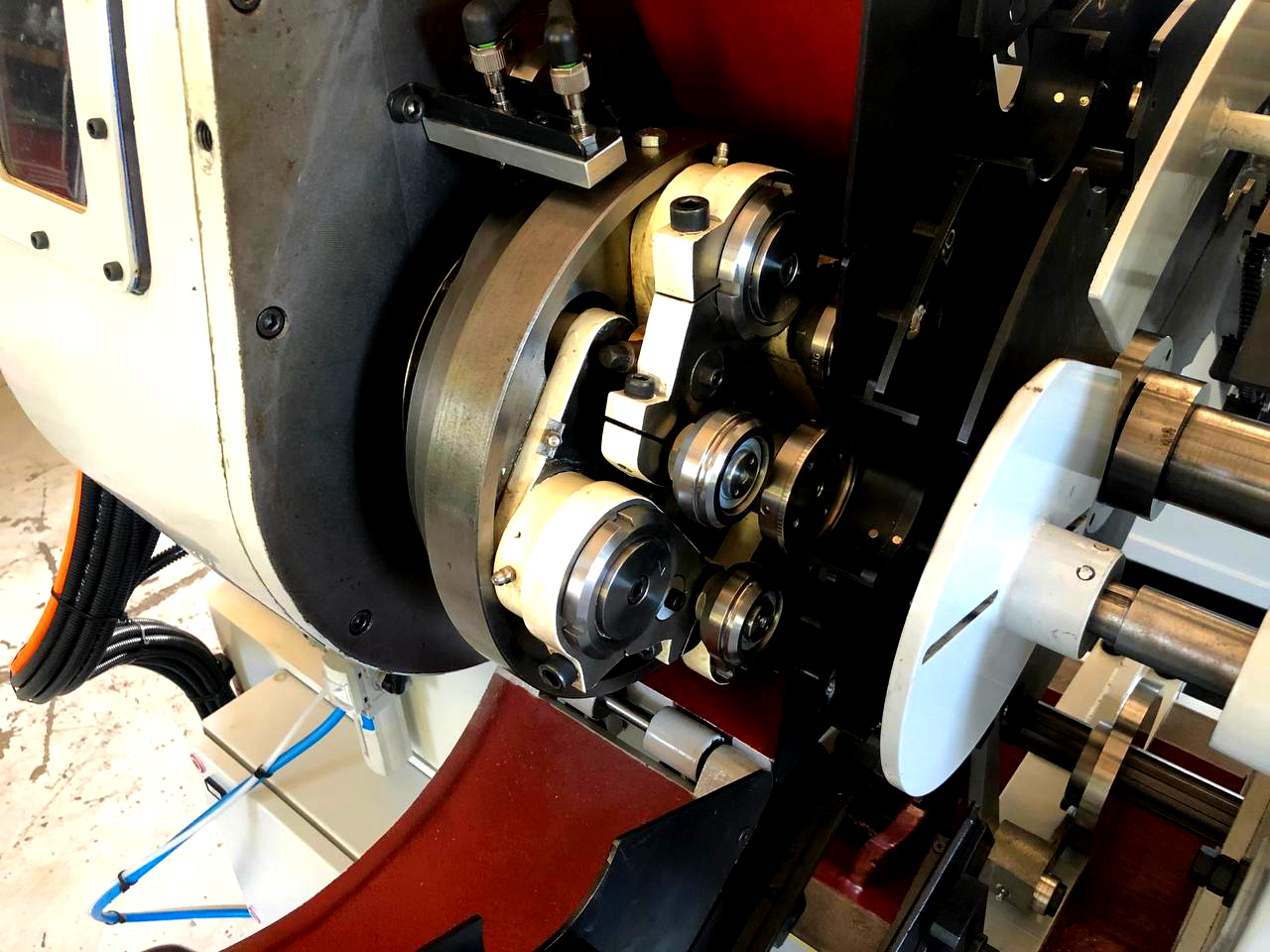
TOOLING CHANGE
The replacements necessary in the event of a change in diameter can be carried out in a maximum of about two hours of work. For the change of can height only, a few adjustments are necessary which take only a few minutes.
TECHNICAL DATA
Max Speed: 80 cans/min
Dimensional limits:
In classic execution: Ø from 66 to 180mm | H from 80 to 400mm
In special execution: Ø from 52 to 193mm | H from 66 to 400mm
Power combined: 9.4 + 9.4 Kw
Max sheet thickness: 0,4mm
Max dimensions: 172 x 220 x 176 cm
“It’s easier to love a brand when the love is reciprocated.”